Alright, let’s dive into my recent adventure with Waters Lab asset utilization. It all started with a simple question: are we really squeezing every last drop of value out of our lab equipment?
So, first thing I did was create a damn spreadsheet. Yep, old school. Listed every piece of equipment – from the fancy mass specs to the humble centrifuges. Then I went around and actually talked to people. Asked them how often they were using stuff, what for, and if there were any bottlenecks. It was a bit like pulling teeth, but I got some good intel.

Next up, data mining! I dove into our lab management system (LIMS). Tried to pull out usage reports, maintenance logs, you name it. The LIMS was a bit of a beast, to be honest. The interface felt like it was designed in the 90s, but after some serious digging, I managed to extract some useful numbers.
Now, for the fun part – analysis. I compared the self-reported usage from my interviews with the LIMS data. Surprise, surprise, there were discrepancies! Some instruments were being used way less than expected. Others were booked solid, creating huge wait times.
Then I started brainstorming solutions. For the underutilized equipment, I suggested opening them up to other departments or even offering services to external researchers. Figured we could at least recoup some of the costs. For the bottlenecked instruments, the easy solution was to buy another one, but I suggested optimizing the workflow first. Maybe better scheduling, better training, or even just streamlining the sample prep process.
I put together a little presentation with my findings and recommendations. Presented it to the lab manager. She was skeptical at first, but the data spoke for itself. We ended up implementing a pilot program to optimize the workflow around one of the bottlenecked instruments. It involved some new SOPs, a bit of cross-training, and a whole lot of communication.
A few weeks later, boom! Wait times were down, throughput was up, and everyone was a little less stressed. It wasn’t a perfect solution, but it was a step in the right direction. And it all started with a damn spreadsheet and a little bit of curiosity.
Lessons learned? Talk to people, trust the data (but verify it!), and don’t be afraid to challenge the status quo. Oh, and learn to love spreadsheets. They’re your friend, even if they don’t always feel like it.
- Step 1: Inventory and Data Gathering (Spreadsheet + Interviews)
- Step 2: Data Mining (LIMS System)
- Step 3: Analysis (Compare Data Sources)
- Step 4: Solution Brainstorming (Internal & External Options)
- Step 5: Presentation and Implementation (Pilot Program)
- Step 6: Measurement and iteration
That’s it for today folks. Happy lab-ing!
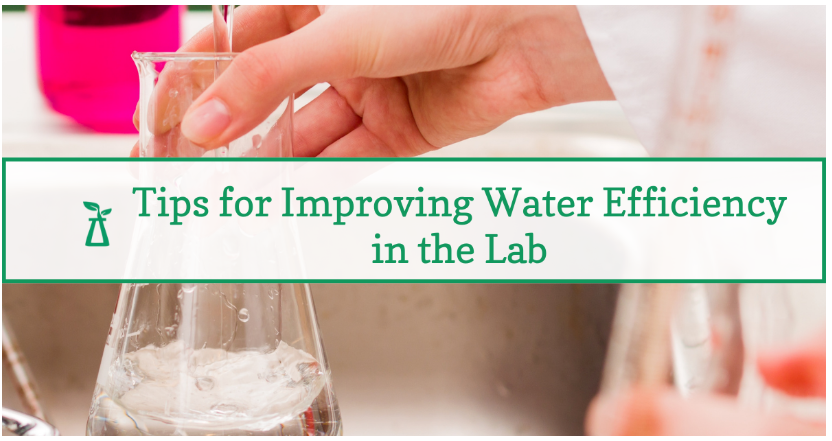